In the elevator manufacturing industry, excellence isn’t just about creating a product—it’s about delivering a solution that works seamlessly from day one. At LJ Elevator, we’ve perfected a process that many manufacturers overlook: pre-assembly and testing before shipment. Did you know that this critical step ensures long-term safety, reliability, and peace of mind for our customers?
Pre-assembly and testing simulate the elevator’s actual installation and operation in the factory, identifying and resolving potential issues before delivery. This meticulous process ensures that the elevator is ready to perform flawlessly upon arrival, saving time, money, and effort.
Let’s explore why pre-assembly and testing matter, how we do it differently, and why it positions LJ Elevator as an industry leader you can trust.
What Is Elevator Pre-Assembly and Testing?
Elevator pre-assembly involves partially or fully assembling the elevator components in our factory to simulate installation. This process ensures all systems—mechanical, electrical, and control—are fully functional and perfectly aligned.
Testing goes a step further. We operate the elevator under simulated real-world conditions, ensuring that every function, from door operation to speed control, meets our rigorous standards. Pre-assembly and testing guarantee that no defects make their way to the customer.
For instance, during this phase, we check for:
- Smooth operation of doors and cabin movement.
- Alignment of key components like traction machines and control systems.
- Safety features, including emergency brakes and overload sensors.
This step ensures our elevators arrive at your site ready for seamless installation.
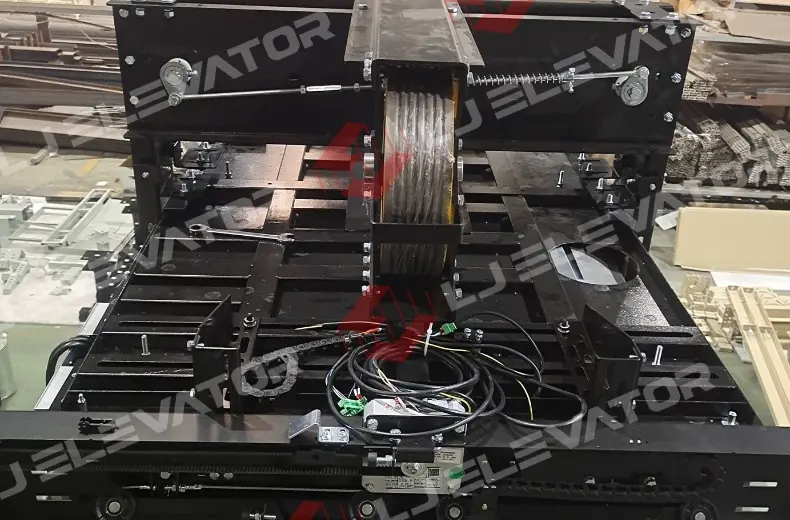
Why Do Many Manufacturers Skip This Crucial Step?
Pre-assembly and testing require time, resources, and expertise. Many manufacturers focus solely on producing components, leaving installation and testing to third-party contractors or post-delivery technicians.
While this approach saves them effort, it shifts the burden of troubleshooting and fine-tuning to the customer. This can lead to delays, additional costs, and a lack of confidence in the product.
At LJ Elevator, we believe this isn’t acceptable. By conducting pre-assembly and testing in-house, we ensure that every product meets our exacting standards before it leaves the factory.
How Does LJ Elevator Set the Standard?
At LJ Elevator, pre-assembly and testing are integral to our manufacturing process. We don’t just build elevators—we ensure they’re ready to perform.
Here’s what sets our process apart:
- Comprehensive Pre-Assembly: Every component is assembled and tested to ensure seamless integration. This includes the cabin, doors, and control systems.
- Simulated Operation Testing: We run the elevator as it would function in a real building. From stopping accuracy to safety feature checks, every detail is verified.
- Labeled Parts for Simplicity: Each part is clearly labeled to help installers quickly find the right components, ensuring a faster and more accurate installation process. This minimizes confusion and risk.
- Transparency Through Video Evidence: For every unit, we record the testing process. Our customers can review the elevator’s performance before it’s shipped, giving them complete confidence in their purchase.
We’ve even encountered situations where customers working with other manufacturers were left with extra parts after installation. These uninstalled components created safety risks and operational issues. Our labeling system ensures this never happens with LJ Elevator products. Request a testing video sample here.
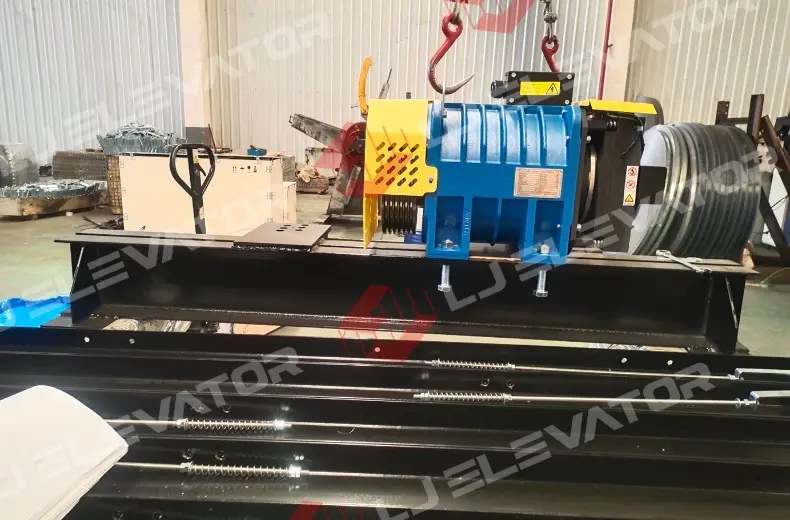
What Are the Benefits of Pre-Assembly and Testing for Customers?
Pre-assembly and testing don’t just enhance product quality—they directly benefit you as the customer. Here’s how:
1. Fewer On-Site Issues
By resolving potential problems during factory testing, we reduce the risk of installation delays or performance issues. This saves time and ensures a smoother handover.
2. Reduced Maintenance Costs
Early detection of issues minimizes the likelihood of costly repairs or adjustments after installation.
3. Enhanced Confidence in Quality
Seeing a fully operational elevator in our testing videos assures customers that they’re investing in a reliable product.
4. Faster Installation with Labeled Parts
Our labeled parts system ensures every piece is installed correctly, preventing confusion and ensuring the elevator operates as intended from day one.
For property developers, building managers, or procurement officers, these advantages translate to greater efficiency, cost savings, and long-term trust.
Why Transparency Matters in Elevator Manufacturing
In an industry where quality and safety are paramount, transparency is everything. At LJ Elevator, we believe our customers deserve to see what they’re paying for. That’s why we record every testing session and share it with you.
These videos show the elevator operating under real-world conditions, highlighting its performance and safety features. It’s this level of openness that sets us apart from manufacturers who skip pre-assembly entirely.
Transparency fosters trust, and trust builds lasting relationships. With LJ Elevator, you’re not just buying an elevator—you’re gaining a partner committed to your success. Learn about our customer-first approach here.
What Questions Should You Ask Your Elevator Manufacturer?
When evaluating elevator manufacturers, consider asking the following:
- Do you conduct pre-assembly and testing for all products?
- How do you ensure the elevator arrives installation-ready?
- Can you provide documentation or videos of the testing process?
- What issues do your testing procedures address?
- How does your process reduce on-site troubleshooting?
- Do you have systems in place to simplify installation, such as labeled parts?
These questions help identify companies that prioritize quality, transparency, and customer support—qualities LJ Elevator exemplifies.
Why Choose LJ Elevator?
At LJ Elevator, our commitment to pre-assembly and testing isn’t just a process—it’s a promise. Here’s what you can expect when you work with us:
- Rigorous Quality Control: Every elevator undergoes detailed inspections and testing to ensure flawless operation.
- Customer-Centric Transparency: Video recordings of the testing process provide peace of mind.
- Labeled Components: Each part is clearly marked to streamline installation and ensure safety.
- Enhanced Safety Standards: We test all safety features, from emergency brakes to overload sensors, before shipment.
- Streamlined Installation: Pre-assembled components reduce installation time and costs.
Conclusion
Pre-assembly and testing are more than just a step in our manufacturing process—they’re the foundation of our commitment to quality. At LJ Elevator, we go the extra mile to ensure every elevator meets our high standards, giving you a product that’s safe, reliable, and installation-ready.
Our meticulous labeling system further simplifies installation, ensuring your elevator operates perfectly from the start. Experience the difference meticulous testing makes. Contact us today to learn more about our products and processes. Let’s elevate your building together with solutions you can trust!