Have you ever ridden in an elevator and noticed uneven seams on the car panels and slight deformation on the surface? These imperfections, while subtle, detract from the premium feel of a high-end elevator. What if there was a process that could eliminate these imperfections and smooth the seams of the elevator car? At LJ Elevator, we use advanced grooving technology to solve this problem.
We pre-cut V-grooves in the steel plate before bending it, minimizing R-angles and allowing for smaller seams during installation. This technique results in cleaner lines, smaller gaps, and a flawless appearance that can’t be achieved with traditional bending processes.
Want to know how it works? Come along with LJ Elevator and discover how we did it.
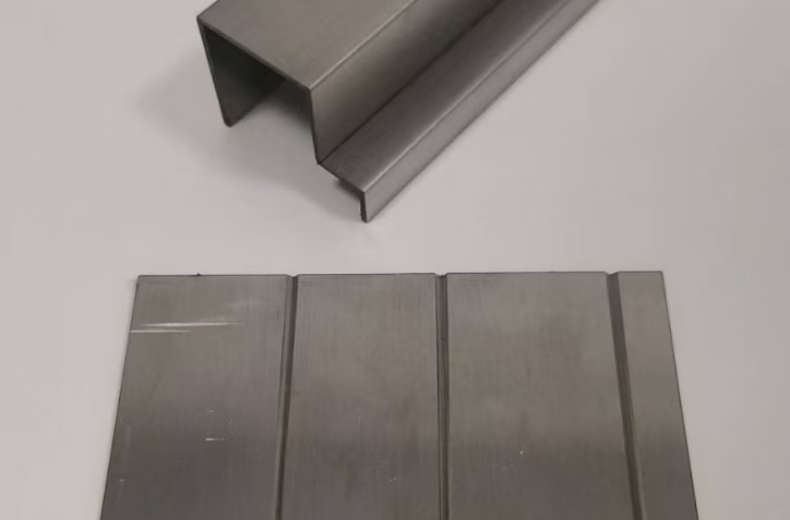
What Are the Limitations of Traditional Bending?
Traditional elevator panel manufacturing relies on common bending techniques, which have several significant drawbacks:
1. Excessive R-angle
Due to the thickness and flexibility of the material, rounding (R-angle) occurs on the outside of the bending of steel panels. Conventional bending with an R-angle of ≥ 2 mm makes the edge look as if it will split immediately.
2. Uneven Gaps Between Panels
After bending, even small deviations can lead to inconsistent panel alignment. The gap between panels fluctuates between 1-3 mm and needs to be manually adjusted during installation. This inconsistency can spoil the visual sense of the interior of the elevator car.
3. Surface Imperfections and Stress Marks
Conventional bending creates stress points that result in minor surface distortions, corrugations or indentations. When exposed to light, these defects can become very visible, reducing the perceived quality of the elevator.
At LJ Elevator, we viewed these challenges as opportunities for innovation, resulting in the implementation of a precision-driven grooving process.
How Does the Grooving Process Work?
The grooving process involves pre-cutting V-grooves in precise locations on the steel sheet before bending it. By removing a portion of the material thickness (typically 1/3 of the plate thickness), the plate is bent with an R-angle close to 90 degrees.
This process ensures that the steel will bend without cracking, distorting or creating large R angles. The result? Perfect alignment and a premium, modern look.
The Four Core Advantages of Grooving
1. Sharper Aesthetic: R Angles Below 0.5mm
Grooving technology reduces the R angle from the traditional 2mm to as low as 0.3-0.5mm. This precision creates a near-right-angle appearance, producing sleek, geometric lines that perfectly match modern elevator design.
Case Study:
A luxury hotel project tested our grooved panels and found that edge clarity improved by 60%, while light reflections created a richer, more dynamic look.
2. Seamless Splicing: Gap Error ≤0.2mm
With traditional methods, panel gaps are unpredictable, often requiring labor-intensive manual adjustments during installation. In contrast, grooving ensures consistent edge alignment, keeping gaps as tight as ≤0.2mm—a difference that is nearly invisible to the naked eye.
Experimental Comparison:
- Traditional process: 1.5mm average segment gap
- Grooving process: ≤0.2mm gap (precision improvement of over 85%)
With such high accuracy, grooved panels create a cleaner, more unified elevator interior.
3. Strength Meets Precision: A More Durable Structure
Some assume that grooving weakens the steel plate, but in reality, the V-shaped cut optimizes stress distribution during bending. This prevents material fatigue, making the final structure stronger and more resilient.
Lab Test Results:
Independent testing found that grooved bending increases fatigue strength by 18%, ensuring that panels maintain their form even after years of use.
This means:
- No warping over time
- Increased durability for long-term installations
- High resistance to stress and impact
4. Faster, More Precise Installation: Saving 30% of Labor Time
Because grooved panels fit together with micron-level precision, installation is faster, easier, and requires fewer manual adjustments. This streamlines the assembly process and reduces dependency on skilled labor.
Project Data:
A super high-rise project using grooved panels saw a 25% reduction in installation time and zero rework cases, demonstrating its efficiency.
How Grooving Elevates the Entire Elevator Industry
The benefits of grooving extend beyond just looks—it represents a fundamental shift in elevator manufacturing.
1. Expanded Design Possibilities
Grooved bending allows for:
- Acute angle bends
- Multi-segment curves
- More intricate, customized designs
This flexibility unlocks new creative potential for high-end, luxury elevator interiors.
2. Premium Perceived Quality
When passengers step into an elevator with ultra-precise paneling, they subconsciously associate it with luxury and high quality—just like stepping into a high-end car or luxury hotel lobby.
3. Reduced Maintenance and Long-Term Value
- Less wear and tear due to precise manufacturing
- Fewer alignment issues over time
- Lower maintenance costs, improving the total lifecycle value of the elevator
FAQs About the Grooving Process
1. Does grooving weaken the steel plate?
No. The process enhances stress distribution, making the structure more durable over time.
2. Can grooving be applied to all types of elevator cars?
Yes, it is suitable for passenger, freight, and panoramic elevators, among others.
3. How does grooving impact installation costs?
By improving panel accuracy, grooving reduces the need for on-site adjustments, cutting installation time by up to 30%.
4. Is grooving more expensive than traditional bending?
While the initial process cost is slightly higher, the long-term savings in labor and maintenance outweigh the cost difference.
5. Why don’t all manufacturers use grooving?
It requires advanced machinery and expertise. At LJ Elevator, we prioritize innovation, ensuring every car meets the highest precision standards.
Conclusion:
At LJ Elevator, we don’t just make elevators, we’re committed to innovation, and that’s why architects, developers and property managers trust us. We go beyond traditional bending methods to deliver virtually invisible panel seams and structurally stronger elevator cabs.
Contact us today to learn more about our precision grooving process and more benefits of our elevators.